Little Known Facts About Alcast Company.
Little Known Facts About Alcast Company.
Blog Article
Alcast Company Things To Know Before You Buy
Table of ContentsSome Known Questions About Alcast Company.The Ultimate Guide To Alcast CompanyThe Ultimate Guide To Alcast CompanyAlcast Company Things To Know Before You BuyAll about Alcast CompanyThe Main Principles Of Alcast Company
Chemical Comparison of Cast Aluminum Alloys Silicon advertises castability by minimizing the alloy's melting temperature and enhancing fluidity throughout spreading. Furthermore, silicon adds to the alloy's toughness and use resistance, making it beneficial in applications where longevity is crucial, such as auto parts and engine parts.It likewise enhances the machinability of the alloy, making it much easier to process right into completed items. In this means, iron contributes to the total workability of aluminum alloys. Copper boosts electric conductivity, making it beneficial in electrical applications. It also enhances deterioration resistance and contributes to the alloy's overall strength.
Manganese adds to the stamina of light weight aluminum alloys and boosts workability (Aluminum Casting). It is typically made use of in wrought light weight aluminum items like sheets, extrusions, and profiles. The existence of manganese help in the alloy's formability and resistance to breaking throughout manufacture procedures. Magnesium is a light-weight component that supplies stamina and influence resistance to aluminum alloys.
The smart Trick of Alcast Company That Nobody is Discussing
Zinc enhances the castability of aluminum alloys and aids regulate the solidification procedure throughout spreading. It boosts the alloy's strength and firmness.

The primary thermal conductivity, tensile stamina, yield stamina, and prolongation differ. Among the above alloys, A356 has the greatest thermal conductivity, and A380 and ADC12 have the cheapest.
More About Alcast Company
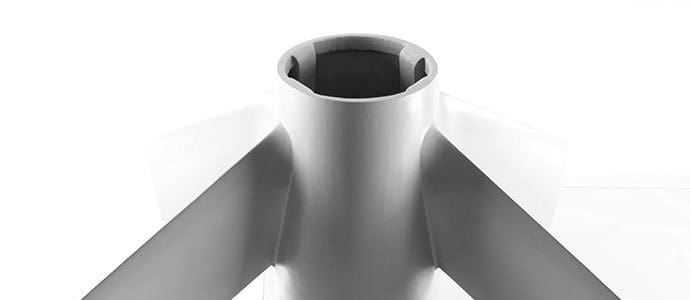
In accuracy casting, 6063 is fit for applications where elaborate geometries and top quality surface area finishes are vital. Instances consist of telecommunication enclosures, where the alloy's remarkable formability permits smooth and aesthetically pleasing styles while keeping architectural stability. Similarly, in the Illumination Solutions sector, precision-cast 6063 components create stylish and efficient illumination fixtures that need detailed shapes and excellent thermal performance.
It leads to a better surface area coating and much better corrosion resistance in A360. In addition, the A360 shows superior elongation, making it ideal for complex and thin-walled components. In precision casting applications, A360 is well-suited for industries such as Customer Electronics, Telecommunication, and Power Tools. Its enhanced fluidity enables elaborate, high-precision components like smartphone cases and interaction gadget housings.
Getting My Alcast Company To Work
Its one-of-a-kind buildings make A360 a beneficial selection for precision casting in these sectors, improving item toughness and quality. Aluminum alloy 380, or A380, is an extensively used spreading alloy with numerous distinctive features. It offers exceptional castability, making it an ideal option for precision casting. A380 displays excellent fluidness when molten, guaranteeing complex and thorough mold and mildews are accurately recreated.
In precision casting, light weight aluminum 413 beams in the Customer Electronic Devices and Power Equipment markets. It's frequently utilized to craft detailed parts like smartphone housings, video camera bodies, and power device coverings. Its accuracy is impressive, with limited resistances as much as 0.01 mm, making sure my blog perfect product assembly. This alloy's exceptional corrosion resistance makes it an outstanding choice for outdoor applications, ensuring lasting, long lasting products in the discussed sectors.
Little Known Questions About Alcast Company.
Once you have actually decided that the light weight aluminum pass away casting procedure is ideal for your job, an important next step is selecting one of the most suitable alloy. The light weight aluminum alloy you choose will significantly influence both the casting process and the residential properties of the end product. Due to this, you have to make your decision thoroughly and take an educated technique.
Identifying the most suitable light weight aluminum alloy for your application will imply weighing a vast range of qualities. The first classification addresses alloy attributes that affect the manufacturing procedure.
Our Alcast Company Ideas
The alloy you select for die casting directly influences a number of facets of the casting procedure, like just how simple the alloy is to collaborate with and if it is vulnerable to casting problems. Warm cracking, likewise referred to as solidification breaking, is a regular die casting flaw for light weight aluminum alloys that can lead to inner or surface-level tears or fractures.
Specific light weight aluminum alloys are extra prone to warm cracking than others, and your selection must consider this. It can harm both the actors and the die, so you need to look for alloys with high anti-soldering properties.
Corrosion resistance, which is already a significant quality of light weight aluminum, can differ substantially from alloy to alloy and is an essential characteristic to take into consideration depending upon the environmental conditions your product will be exposed to (aluminum metal casting). Put on resistance is an additional home typically sought in aluminum items and can set apart some alloys
Report this page